
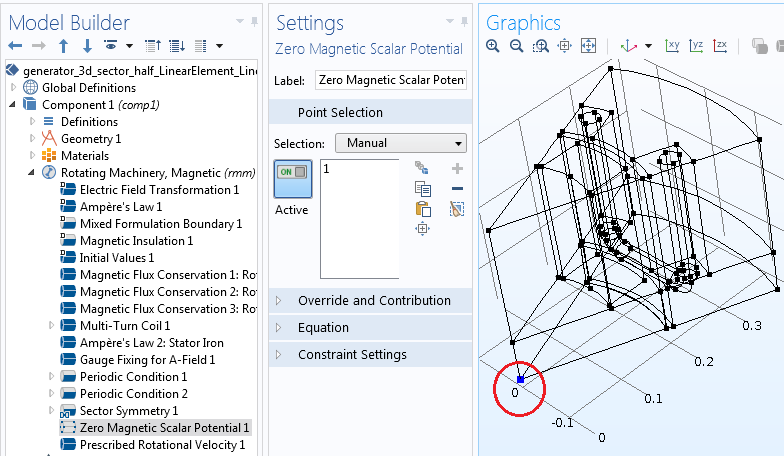
- Rotating machinery laminar flow comsol 5.3 how to#
- Rotating machinery laminar flow comsol 5.3 software#
Rotating machinery laminar flow comsol 5.3 software#
After applying one of these features, the COMSOL Multiphysics software will enable moving mesh for the selected domains and the set-up of the appropriate transformations of the electromagnetic field. Use the Prescribed Rotation feature to specify an angle of rotation (which can be time dependent) or the Prescribed Rotational Velocity feature to enter a constant angular velocity. We can now define the dynamics of the system using the Rotating Machinery, Magnetic interface. Watch a video to learn more about using Form Assembly in rotating machinery models. During rotation, the meshes slide on each other, remaining in contact at the pair. The boundaries highlighted in blue are collected in an identity pair. The rotating and stationary parts are meshed separately, as indicated by the different positions of the mesh nodes on the two sides. During finalization, an identity pair is automatically created under Definitions, identifying the common (contacting) boundaries of the two objects.Ī close-up of the DC motor’s mesh. Then, choose Form Assembly in the finalization node of the geometry sequence. Using unions and other operations, create a single geometry object for the stationary part and another one for the rotating part. To mesh the two parts separately, the objects must be finalized by forming an assembly. Red represents a possible choice for the cut boundary.īy default, the last step in a geometry sequence is to finalize by forming a union, uniting all of the geometrical objects and meshing them as a single object.
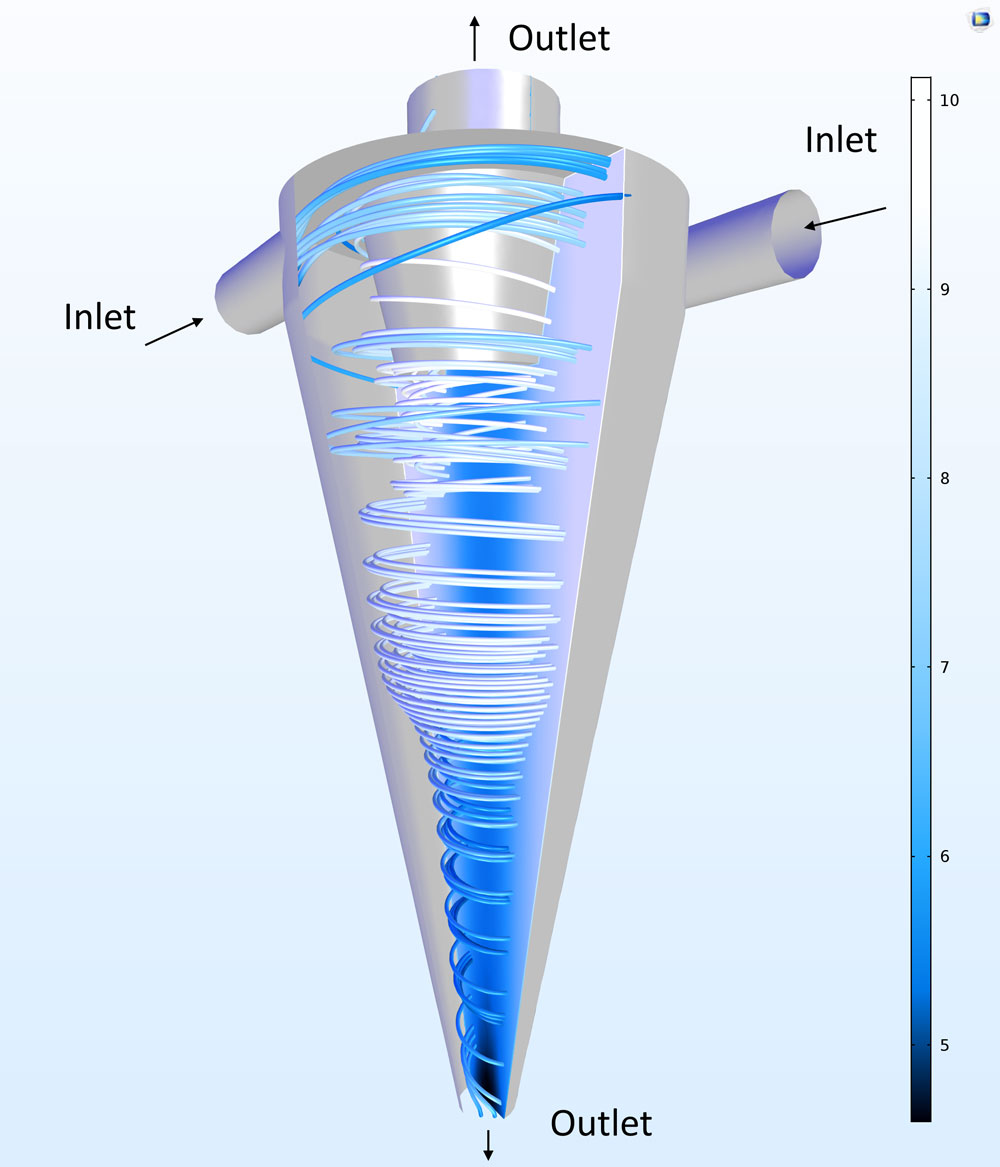
The geometry must include the air region between the magnets. The two parts with the corresponding meshes are always in contact at the cut boundary. During simulation, the part containing the stator remains stationary while the part containing the rotor moves. The two parts are then meshed separately. The machine’s geometry is cut (usually along the air gap) into two parts: one containing the stator, and one containing the rotor. Geometry of a DC commutated motor that includes two permanent magnets and a rotating winding. The Rotating Machinery, Magnetic interface uses the moving mesh approach to model this rotation, as the finite element method does not support rotations. In any rotating magnetic machine, there are two parts: the stator and the rotor, separated by an air gap enabling the rotor’s rotation.
Rotating machinery laminar flow comsol 5.3 how to#
Follow along as we explore how to model rotating machinery and detail best practices for working with this feature. The Rotating Machinery, Magnetic physics interface in COMSOL Multiphysics is designed specifically for modeling these systems. Among the different types of electrical machines, rotating machines such as generators and motors take up a central role. Electrical machines are an important pillar in modern industrial society.
